1
RECEIVING ORDERS
Weighing equipment and identifying part numbers.
2
CONTROL & COMPLIANCE BEFORE TREATMENT
Checking the suitability of products for galvanizing :
Surface finish, dimensions, design, holes.
Quantity control according to customer purchase order.
Customer contact in case of compliance.
3
HOOKING
Use the right tools for each part (round irons, chains, multi-hooks, etc.).
Optimization of drill hole positioning.
4
DEGREASING
Its purpose is to remove all dirt and grease that would prevent the dissolution of surface iron oxides.
5
RINSING
Rinsing is carried out after degreasing to avoid polluting subsequent operations.
6
SCAPING
Its purpose is to remove scale and other oxides from the steel surface.
Pickling is carried out in a dilute hydrochloric acid solution at room temperature, with the addition of an inhibitor to prevent the steel from attacking once its oxides have been removed.
7
RINSING
Rinsing is also carried out after stripping to remove iron salts and traces of acid that could contaminate the next operation.
8
FLUXING
It prevents the steel from reoxidizing before entering the zinc bath. Flux decomposition also promotes the iron/zinc metallurgical reaction when the part is immersed in the zinc bath.
9
DRYING
Drying is carried out in an oven to avoid zinc splashes when the part is immersed.
10
GALVANIZING
The parts are then immersed in the molten zinc bath at 450°C. Immersion times vary according to the load, size and thickness of the parts: from 3 to 4 minutes for simple shapes, to 10 to 15 minutes for massive assemblies or large hollow bodies.
11
COOLING & QUALITY CONTROL
Visual inspection on leaving the zinc bath (appearance, deformation, etc.).
Thickness control by sampling.
Inspection report issued on request, in accordance with NF EN ISO 1461.
The advantages of galvanizing
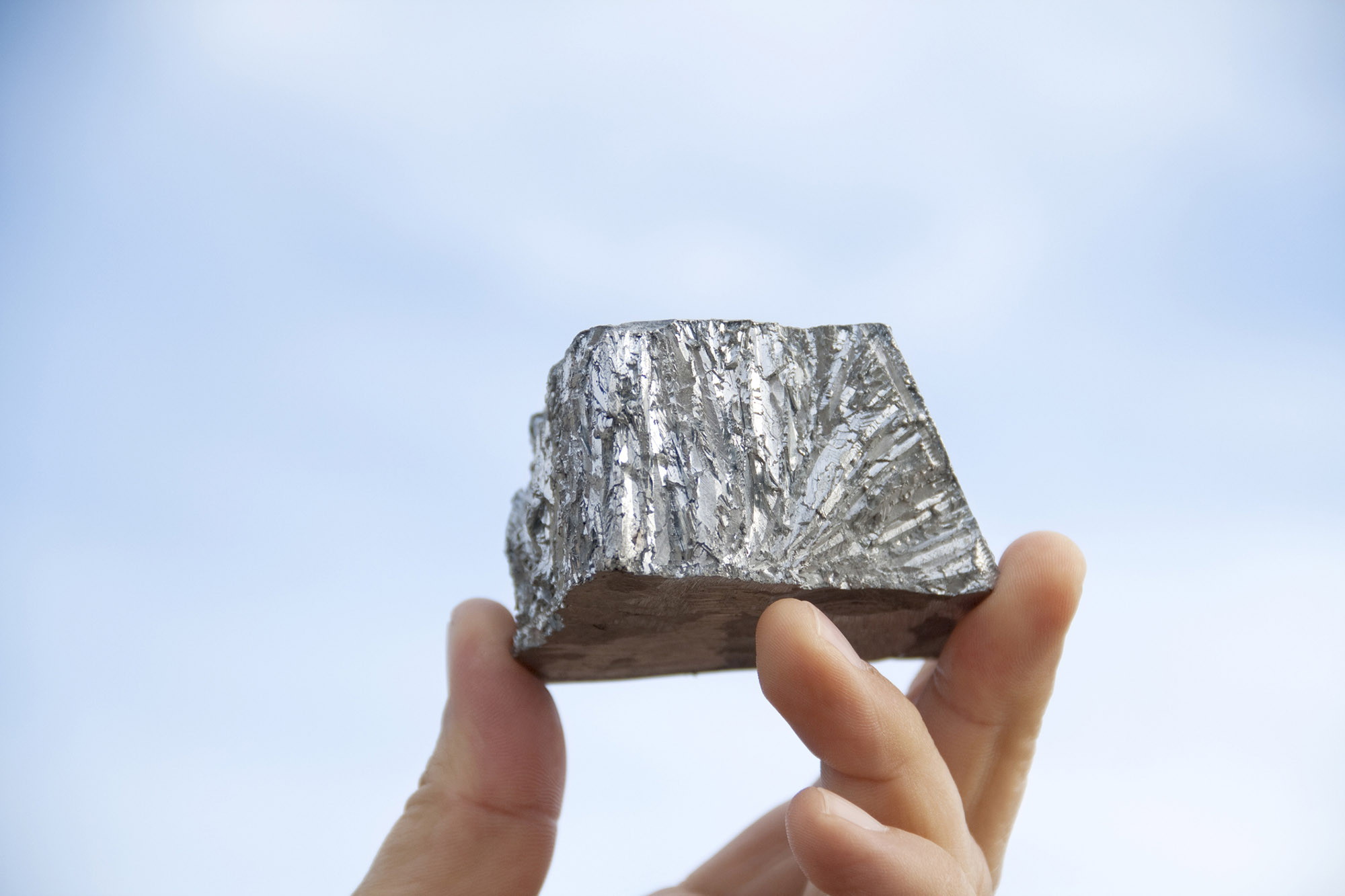
An aesthetic and durable choice that enhances a structure
Raw galvanized steel is an aesthetically pleasing material. To enhance architectural harmony, it can be painted in the color of your choice.
Ready-to-use products
Once galvanized, a part is easy to transport and install, whatever the weather conditions.
An industry that offers technical assistance
A galvanizer is an industrialist who listens to you: involve him right from the design stage of your part or structure, so that he can advise you on the right materials and the right application.
A highly cost-effective solution
Over a service life of around 30 years, hot-dip galvanizing is around half the cost of other systems, whatever their initial cost.
Exceptionally long, maintenance-free service life
A hot-dip galvanized part is maintenance-free for over 30 years, under normal conditions of use.
Integral part protection
A hot-dip galvanized part is fully protected: on the outside and in inaccessible places (hollow bodies, tubes, etc.) that other processes cannot reach. This guarantees complete anti-corrosion protection.
Remarkable mechanical properties
The surface of a hot-dip galvanized steel part is made up of several zinc-iron intermetallic layers that are harder than steel. This coating offers exceptional strength and good adhesion.
Doubly protected products
Hot-dip galvanizing offers double protection for steel: physical protection (a barrier screen that isolates the steel) and electrochemical protection (a cathodic effect that prevents corrosion from spreading in the event of surface injury).
Effective anti-corrosion guarantees
Post-manufacture galvanizing is guaranteed for over 10 years against corrosion. Some carmakers who use galvanized steel offer a 12 to 15-year warranty. These figures are purely indicative and are not contractually binding. Guarantees may be granted on a case-by-case basis by galvanizing manufacturers.
Perfectly recyclable products
Like steel, the zinc used to protect this metal through galvanizing is recyclable. It comes from nature and can be reused indefinitely, while retaining its properties.
Standards and designs
Choice of steels before galvanizing
It is necessary to impose specifications to ensure compliance with these two elements. Standard NF A 35-503 “Aciers pour galvanisation par immersion à chaud” defines three categories of steel according to their guaranteed silicon and phosphorus content. You can obtain this guarantee by asking your steel supplier to provide you with a product inspection document in accordance with NF EN 10204: certificat de réception 3.1A.
NF EN ISO 1461: Hot-dip galvanizing coatings on finished cast-iron and steel products.
It defines the properties and characteristics of hot-dip galvanizing coatings, with test methods for checking zinc thickness per unit area, appearance and adhesion, and conformity criteria.
NF EN ISO 14713 : Zinc coatings. Guidelines and recommendations for corrosion protection of iron and steel in buildings.
It completes the precautions to be taken on the design of parts to obtain good quality galvanized coatings and specifies the related techniques after galvanization.
NF A 35-503 : Steel products. Requirements for hot-dip galvanizing of steel components.
This standard sets out the chemical characteristics to be met by steels intended for hot-dip galvanizing. It specifies three grades of steel suitable for galvanizing.
NF EN 1090 : Construction of steel structures. Successfully obtained by CTICM in 2018.
Hollow body drilling chart
Hot-dip galvanizing: Your insurance against corrosion
For over 150 years, hot-dip galvanizing has been the most reliable and durable method of protecting steel against corrosion.
Key points :
- Durability and Reliability :
- Mariage Naturel : Hot-dip galvanizing combines steel and zinc for optimum corrosion protection, proven for over 150 years.
- Reliable coating : With hot-dip galvanizing, the quality of the work is immediately visible, guaranteeing a flawless coating.
- Dialogue and comprehension :
- Classes E and F : Promoting dialogue between specifiers, builders and galvanizers is essential. The choice between class E (aesthetic) and class F (functional) ensures that the end result meets expectations.
- 30-year warranty :
- Maintenance-free : Galvazinc member galvanizers offer up to a 30-year warranty, ensuring maintenance-free peace of mind.
- Tradition and know-how :
- Héritage : French galvanizers draw on a long tradition and expertise that has been championed by the Galvazinc association since 1956.
- Continuous Improvement :
- Progress : Galvazinc members are committed to continuous improvement in logistics and quality control to meet customer needs.
- Infinite reuse :
- Circularity : The hot-dip galvanized steel is 100% circular, allowing endless re-use thanks to an adapted design..
Conclusion : Hot-dip galvanizing is the ultimate solution for protecting steel against corrosion, offering durability, reliability and a 30-year warranty. With a tradition of know-how and a commitment to continuous improvement, Galvazinc’s member galvanizers ensure total customer satisfaction and infinite reuse of materials.
Our complementary services
Parts compliance
Drilling
Completion
Before painting
Thread protection
Savings
Certificate of conformity
Hot-dip galvanizing EN ISO 1461
Thickness measurement
Inspection report
Sales of complementary products
Marker and felt suitable for galvanizing
Sales of complementary products
Savings products
Sales of complementary products
Zinc-rich paint to EN ISO 1461 standard
If you have any questions, please do not hesitate to contact us.